Завідувач відділу, доктор технічних наук, професор
Відділ фізико-металургійних процесів наплавлення зносостійких і жароміцних сталей
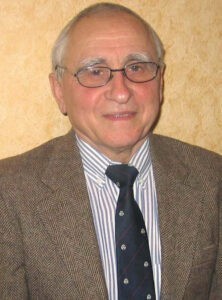
Рябцев Ігор Олександрович
Склад відділу
Загальна чисельність працівників 13, у тому числі:
- 2 – доктора наук;
- 7 – кандидатів технічних наук
- 1Рябцев Ігор Олександрович
Завідувач відділу, доктор технічних наук, професор
- Teл: +380 44 205-21-80
- E-mail: ryabtsev39@gmail.com
- 2Лентюгов Іван Павлович
Заступник завідувача відділу
- Teл: +380 44 205-25-20
- E-mail: gavs04@ukr.net
- 3Кусков Юрій Михайлович
Провідний науковий співробітник
- Teл: +380 44 205-25-22
- 4Перепльотчиков Євген Федорович
Провідний науковий співробітник
- Teл: +380 44 205-23-25
- 5Бабінец Анатолій Анатолійович
Старшій науковий співробітник
- Teл: +380 44 205-20-37
- E-mail: a_babinets@ukr.net
- 6Кондратьєв Ігор Олександрович
Старшій науковий співробітник
Teл.: +380 44 205-20-37
- 7Кузьменко Олег Геннадійович
Старшій науковий співробітник
- Teл.: +380 44 205-21-31
- E-mail: 58kuzmenko@ukr.net
- 8Рябцев Ігор Ігорович
Старшій науковий співробітник
Teл.: +38 044 205-25-22
- 9Осін Владіслав Володимирович
Науковий співробітник
Teл.: +380 44 205-21-31
Відділ було організовано у 1954 році.
– дослідження методів легування наплавленого металу і на цій основі розробка нових матеріалів для наплавлення (порошкові та суцільні дроти, порошкові і суцільні стрічки, порошки, флюси та ін.);
– дослідження особливостей зношування, які визначають термін експлуатації наплавлених деталей у різних галузях промисловості;
– дослідження напружено-деформованого і структурного стану наплавлених деталей (стосовно до різних способів наплавлення), а також їх опору в процесі експлуатації одночасної дії зношування і циклічних термічних і механічних навантажень;
– розробка енерго- і ресурсозберігаючих технологій наплавлення нових та відновлення зношених деталей, робочих органів машин і механізмів, інструментів та ін., які експлуатуються в умовах різних видів зношування та циклічних силових і термічних навантажень;
– розробка універсального і спеціалізованого обладнання для автоматичного наплавлення.
- Дослідження впливу мікролегування та модифікування на формування структури високолегованого наплавленого металу, стійкого проти зношувань та циклічних термосилових навантажень (2021-2023 рр.)
- Дослідження закономірностей втомного руйнування багатошарового матеріалу, сформованого наплавленням зносостійких та конструкційних сталей, при виготовлені і відновленні виробів з вуглецевих сталей (2017-2021 рр.)
- Вибрати матеріали і розробити технології електрошлакового наплавлення швидкозношувальних деталей дробильно-розмельного устаткування кар’єрів та дорожньо-будівельної техніки (2021-2025 рр.)
- Розробити порошкові дроти та технології дугового відновлювального наплавлення деталей типу “вал” (вісь) порожнього або суцільного перетину для продовження терміну їх експлуатації (2021-2025 рр.)
- Обладнання, технологія та матеріали для одношарового антикорозійного електрошлакового наплавлення стрічками.
Спільно з КУІС ім. Є.О. Патона розроблено обладнання і технологія антикорозійного електрошлакового наплавлення стрічками (рис.).
Рисунок – Схема процесу (а) і установка для ЕШН двома стрічками (б): 1 – електродні стрічки;
2 – ролики, що подають стрічку; 3 – мідна вставка для підведення струму; 4 – флюс; 5 – шлакова ванна; 6 – чавунна ванна; 7 – наплавлений метал; 8 – шлакова кірка; 9 – деталь, що наплавляється.
Досліджено вплив струму, напруги та швидкості наплавлення, а також величини зазору між стрічками на стабільність електрошлакового процесу, геометричні розміри наплавлених валиків і частку основного металу в наплавленого металу. В експериментах були використані нержавіючі стрічки перетином 0,5х60 мм. Визначено область режимів наплавлення двома стрічками, при яких забезпечується висока продуктивність і стійкий електрошлаковий процес з хорошим формуванням наплавленого і мінімальним проплавленням основного металу в межах 7… 9%: Iн = 1400…1500 A; Uн = 32…33 В; Vн = 14…17 м / год; зазор між стрічками – 16 мм. Механічні властивості металу, наплавленого на цих режимах знаходяться на рівні механічних властивостей стали 309LNb.
Призначення та області застосування: Отримані результати можуть бути використані при виборі або розробці матеріалів і технологій антикорозійного наплавлення деталей енергетичного та хімічного обладнання.
- Технологія і матеріали для зносостійкого одно- або багатошарового дугового наплавлення тонких сталевих пластин або листів (≤ 5 мм).
Розроблено технологію дугового наплавлення і порошкові дроти невеликого діаметра (Ø 1,4-1,6 мм) для дугового наплавлення тонких сталевих пластин і листів (рис.).
Рисунок – Наплавлені сталеві пластини загальною товщиною 4 + 6 мм, які підготовлені для проведення випробувань ударними навантаженнями високої інтенсивності.
Основні технічні характеристики та переваги технології:
– можливість якісного наплавлення без пропалив та інших дефектів тонких сталевих пластин або листів;
– широкий спектр властивостей наплавлених листів в залежності від вибору типу наплавленого металу (зносостійкість при різних видах абразивного зношування, корозійна стійкість в різних середовищах, здатність протистояти динамічним навантаженням високої інтенсивності та ін.);
– підвищення в 2-3 рази терміну експлуатації наплавлених деталей.
Призначення та області застосування: наплавлені тонкі біметалічні листи призначені для використання в якості футерувальних елементів для підвищення довговічності течок, грохотів, бункерів, кузовів кар’єрних самоскидів, лопатив і покривних дисків роторів тягодуттєвих машин і ін. Багатошарові наплавлені пластини можуть використовуватися в якості засобів індивідуального броне захисту. Гірничодобувна і металургійна галузь народного господарства України.
3. Дугове наплавлення сталевих прокатних валків.
Розроблено технології і матеріали для дугового наплавлення сталевих валків гарячої прокатки різних станів. Дугове наплавлення дозволяє багаторазово і з високою продуктивністю наносити на валки з середньо- і високовуглецевих низьколегованих сталей (вміст вуглецю до 0,9%) шар високолегованої інструментальної сталі без тріщин, пор і інших дефектів. За допомогою розробленого обладнання можливо отримувати на будь-якій складній поверхні наплавлений шар необхідної товщини (в один або кілька проходів) з мінімальними припущеннями на механічну обробку. Останнє дуже важливо, коли наплавляється зносостійка високолегована сталь. Наплавлення здійснюється з попереднім підігрівом, температура якого визначається матеріалом прокатного валка і його масою. Після наплавлення валок уповільнено охолоджується в термостаті або печі.
Широкий асортимент порошкових дротів, розроблених в ІЕЗ спеціально для наплавлення валків, дає можливість в кожному випадку вибрати оптимальний склад наплавленого металу виходячи з конкретних умов роботи валків, характеру і інтенсивності їх зносу, оброблюваності наплавленого металу, ціни і ін. (Табл.)
Для наплавлення валків використовуються флюси АH-20, АН-26, AH-60, АН-348 та ін. Стійкість наплавлених валків в 1,5-3 рази вище, ніж не наплавлених, в залежності від стану, кліті, і ін. чинників; кількість повторних наплавлень звичайно дорівнює 4-5, але може бути і більше. Завдяки цьому в багато разів збільшується термін служби валків і скорочується їх витрата. Наплавлення дозволяє також подовжувати періоди між переточуваннями і працювати на максимальних діаметрах валків, що підвищує продуктивність станів.
- Електрошлакове наплавлення чавунних прокатних валків.
Розроблена технологія електрошлакового наплавлення застосовується при виготовленні і відновленні чавунних валків станів гарячої і холодної прокатки (діаметром від 40 і до 1000 мм) з гладкою бочкою або з калібрами глибиною не більше 10 мм. Товщина наплавляемого зносостійкого шару від 20 до 100 мм (рис.). Технологія забезпечує отримання двошарових валків з гарантованим з’єднанням основного і плакуючого шарів по всій поверхні. Для наплавлення можуть використовуватися найрізноманітніші за хімічним складом матеріали: високолегований чавун, швидкоріжуча і нержавіюча стали і ін.
Рисунок – Процес електрошлакового наплавлення чавунних прокатних валків
Спосіб дозволяє отримати наплавлені шари товщиною від 20 до 100 мм при продуктивності до 600 кг наплавленого металу на годину. Витрата електроенергії на 1 т наплавленого металу становить 1500…1 700 кВт-год.
Необхідна площа для розміщення основного обладнання – 50 … 100 м2. До його складу входять установка для наплавлення з джерелом живлення й установка для плавлення флюсу. Споживана потужність при наплавленні валків до 500 мм – 300 … 400 кВт, до 1000 мм – 700 … 900 кВт. Витрата води – до 30 м3 / год.
5. Матеріали і технології дугового наплавлення штампів і штампового оснащення
Розроблено матеріали і технології дугового напівавтоматичного наплавлення штампів і штампового оснащення для гарячого і холодного деформування металу. Наплавлення застосовується при виготовленні й ремонті штампів. При виготовленні корпус штампа виготовляється з дешевої вуглецевої або низьколегованої конструкційної сталі.
Наплавлення може проводитися напівавтоматом самозахисним порошковим дротом, що значно спрощує техніку відновлення і зміцнення інструменту, особливо складної форми. Для наплавлення малогабаритних штампів застосовуються апарати для аргонодугового або мікро плазмового зварювання (робочий діапазон струмів 20-60 А). При цьому порошковий дріт служить присадним матеріалом. Для наплавлення розроблена гамма порошкових дротів діаметром 1,8-2,8 мм (таблиця). Залежно від типу штампа і умов його експлуатації може бути обрана оптимальна марка дроту, що дозволяє наплавить шар легованого металу з заданими службовими властивостями (термостійкість, теплостійкість, ударна в’язкість і т.ін.) і твердістю від HRC 45 до HRC 62.
Виробничий досвід показав, що стійкість наплавлених штампів в кілька разів вище стійкості штампів з інструментальних сталей типу 5ХНМ, 30Х2НМФ, 4Х5МФС і т.п. Наплавлення дозволяє істотно знизити витрату інструментальної сталі на виготовлення штампів-дублерів.6. Технологія і матеріали для наплавлення штоків гідроциліндрів
Розроблено порошковий дріт ПП-Нп-30Х20МН і технологія електродугового автоматичного наплавлення штоків гідроциліндрів різних механізмів і машин – кріплень шахтних прохідницьких комбайнів, кар’єрних автосамоскидів і т.ін. Штоки гідроциліндрів виготовляють зі сталей типу 40Х і для захисту від корозії робочу поверхню штоків хромують.
За запропонованою технології наплавлення зношених штоків може проводитися після попередньої механічної обробки робочої поверхні або безпосередньо по хромовому гальванічному покриттю (рис.).
Рисунок – Процес електродугового автоматичного наплавлення штоків гідроциліндрів
Штоки наплавляються в один шар під флюсом АН-26П. Розроблений порошковий дріт забезпечує отримання наплавленого металу системи легування Fe-Cr-Ni-Mo, що має високу корозійну стійкість в першому наплавленому шарі. Шліфування наплавленої поверхні забезпечує необхідну чистоту, а висока корозійна стійкість наплавленого шару виключає операцію хромування. Є досвід наплавлення штоків діаметром від 70 мм і вище.
2016 р. Досліджено особливості одношарового електрошлакового наплавлення двома стрічками з нержавіючих хромонікелевих сталей, встановлені оптимальні режими, які забезпечують високу продуктивність (до 40 кг/год), гарне формування наплавленого металу та мінімальну частку основного металу в наплавленому (≤ 15 %). Структура наплавленого метала – аустеніт с 6 % δ-фериту. Міцність з’єднання шарів на зріз і відрив знаходиться на рівні аналогічних показників для наплавленого металу типу 02Х22Н11Г2Б. Досліджені фізико-металургійні особливості утворення звареного з’єднання при дуговому наплавленні під флюсом, відкритою дугою й у захисних газах порошковими дротами Ø 1,8…2,8 мм. У результаті досліджень визначені залежності між режимами наплавлення й найбільш важливими характеристиками процесу наплавлення – величиною проплавлення та часткою основного металу в наплавленому (ДОМ), а також характером формування й геометричними характеристиками наплавлених валиків. На основі цих досліджень розроблена перша вітчизняна комп’ютерна система керування й контролю режимами наплавлення з рекомендаціями з технології наплавлення конкретної деталі.
2017 р. Розроблено технологію плазмово-порошкового наплавлення нікелевих сплавів на низьколеговані сталі і подальшої термічної обробки наплавлених деталей, які забезпечують отримання зварного з’єднання з мінімальним проплавленням основного металу та високими властивостями наплавленого металу. При ЕШН визначений характер зміни струмів піддону, електроду та кристалізатору при зміні величини заглиблення електрода в шлакову ванну для різних діаметрів електроду та різної глибини шлакової ванни. Підтримка заданого значення величини заглиблення електроду забезпечує необхідну рівномірність і глибину проплавлення деталі, а також мінімальну структурну та хімічну неоднорідність. Розроблені технології та матеріали дугового, плазмово-порошкового й електрошлакового наплавлення пройшли дослідно-промислову перевірку, яка підтвердила, що нові технології дозволили підвищити продуктивність і знизити енергоємність цих способів наплавлення.
2018 р. Досліджено зростання у процесі випробувань втомних тріщин в зразках з вуглецевої сталі зі зносостійким наплавленням при циклічних від нульових навантаженнях. Дослідженнями встановлено, що в середньому зразки основного металу (сталь 40Х) до появи втомних тріщин витримали 1,4.106 циклів. Зразки зі сталі 40Х5ФМС, яка відповідає зі складом зносостійкому наплавленому металу, до появи втомних тріщин витримали 0,65.106 циклів. Зразки зі стали 40Х, які були наплавлені порошковим дротом ПП-Нп-25Х5ФМС, до появи втомних тріщин витримали 0,6.106 циклів. У результаті досліджень розроблено технологію ремонтного наплавлення зразків з втомними тріщинами в наплавленому шарі. Технологія передбачає механічне оброблення тріщин до їх повного видалення і заварку оброблення тільки зносостійким порошковим дротом. Відповідно до розробленої технології була проведена обробка та заварка втомних тріщин в зразках, попередньо випробуваних на втомну довговічність.
2019 р. В результаті досліджень встановлено принципово інший характер розповсюдження втомних тріщин в зразках наплавлених з пластичним підшаром, у порівнянні із зразками без підшару. В даному випадку пластичний матеріал підшару уповільнює ріст втомної тріщини, тим самим підвищуючи довговічність наплавленої конструкції в цілому. Крім того, було підтверджено що характер лінії сплавлення окремих валиків та шарів відіграє важливу роль у процесі втомного руйнування наплавлених деталей, адже тріщини здебільшого розповсюджуються або по межі сплавлення окремих валиків, або безпосередньо біля цієї межі, де, ймовірно, розташована зона хімічної та структурної неоднорідності, що несприятливо впливає на втомну довговічність.
Запропоновано відповідну схему ремонту наплавлених деталей з втомними тріщинами, яка полягає у повному видаленні тріщини та металу навколо неї, та наступному заплавленню утвореної розділки. Спочатку наплавляється пластичний підшар дротом Св-08А, а потім робочий шар легованим порошковим дротом ПП-Нп-25Х5ФМС.
2020 р. Для управління глибиною проплавлення основного металу і часткою основного металу в наплавленому при одношаровому антикорозійному дуговому наплавленні запропоновано використовувати високі швидкості подачі електродного дроту (> 500 м/год), коливання електродного дроту, а також імпульсні процеси. Визначено щільність струму для всіх діаметрів електродних дротів, при якій досягається мінімальне проплавлення основного металу – J ≈ 140±4 А/мм2. Встановлено, що найкраще формування наплавленого металу, найбільш плавне, рівномірне і мінімальне проплавлення спостерігається при частоті коливань електродного дроту N = 45 хв-1, амплітуді коливань електродного дроту А = 25 мм і швидкості наплавлення Vн = 7 м/год.
Розроблено конструкцію заготівок і технологію одношарового плазмово-порошкового наплавлення шиберів і сідел нафтогазових засувок, які експлуатуються в корозійному середовищі з підвищеним вмістом сірководню. Технологія забезпечує вже в першому шарі необхідний хімічний склад і високі корозійні властивості наплавленого металу на основі Ni і Fe.
Госпдоговірна тематика.
За останні п’ять років за госпдоговірною тематикою проводилися науково-дослідні роботи по вдосконаленню зварювально-технологічних властивостей порошкових дротів для наплавлення. Визначені причини поганої відокремлюваності шлакової кірки при використанні порошкових дротів для наплавлення під флюсом і пористості металу, наплавленого самозахисними порошковими дротами.
Вибрані матеріали та розроблено технологію електрошлакового наплавлення локальних зносостійких шарів товщиною 10…30 мм на деталі дробильно-розмельного устаткування кар’єрів та дорожньо-будівельної техніки. Для реалізації розробленої технології в промисловості виготовлено циліндричні кристалізатори Ø 50…80 мм і Ø 150…200 мм та квадратний кристалізатор 200х200 мм.
В результаті досліджень розроблено технології плазмово-порошкового та дугового зносостійкого наплавлення на деталі з міді М1 сплавів на основі заліза, нікелю та кобальту. Проведено дугове наплавлення в середовищі захисних газів рильної частини доменної фурми з міді за розробленою технологією наплавлення дротом на основі нікелю. Підготовлено технічну документацію за результатами досліджень та експериментів з наплавлення на мідні зразки обраними зносостійкими наплавлювальними матеріалами.
За контрактом з КНР розроблено і виготовлено обладнання та впроваджена одношарова високопродуктивна технологія ЕШН двома нержавіючими стрічками.
Експериментальні та теоретичні (розрахункові) дослідження напружено-деформованого і структурного стану наплавлених деталей, а також їх опору одночасному впливу різних видів зношування і циклічних термічних і механічних навантажень в процесі експлуатації (стосовно до різних способів наплавлення).
Розробка методів регулювання структури і властивостей наплавленого металу при різних методах наплавлення на основі дослідження ефектів модифікування та мікролегування, а також структурної спадковості в системі електродний (присадний) матеріал-зварювальний ванна-наплавлений метал.
Дослідження особливостей зварюваності при наплавленні високолегованих зносостійких сталей і сплавів на нелеговані та низьколеговані конструкційні стали.
Дослідження і розробка методів регулювання проплавлення основного металу при різних способах наплавлення з метою оптимізації конструкції багатошарових наплавлених деталей.
- Гладкий П.В., Переплетчиков Е.Ф., Рябцев И.А. Плазменная наплавка. – Киев: Экотехнология, 2007. – 292 с.
- Рябцев И.А., Сенченков И.К. Теория и практика наплавочных работ. – Киев: Экотехнология, 2013. – 400 с.
- Рябцев И.А., Сенченков И.К., Турык Э.В. Наплавка. Материалы, технологии, математическое моделирование г. Гливице (Gliwice), Польша: Издательство Силезского поли-технического института (Wydawnictwo Politechniki Śląskiej), 2015. – 590 с.
- Кусков Ю.М., Рябцев И.А., Кузьменко О.Г., Лентюгов И.П. Электрошлаковые технологии наплавки и рециклинга металлических и металлосодержащих отходов. – Киев: Интерсервис, 2020. – 288 с.
- Рябцев И.А., Демченко Ю.В., Панфилов А.И. Износостойкий и коррозионностойкий биметалл. – Киев: ИЭС им Е.О. Патона, 2020. – 224 с.
- Рябцев И.А., Соловьев В.Г., Ланкин Ю.Н., Бабинец А.А. (2017) Компьютерная система автоматического управления процессами дуговой наплавки электродными проволоками. Автоматическая сварка, 5-6, 43–45. https://doi.org/10.15407/as2017.06.07
- Кусков Ю.М., Соловьев В.Г., Лентюгов И.П., Жданов В.А. (2018) Роль шлаковой ванны в процессе наплавки в токоподводящем кристаллизаторе. Современная электрометаллургия, 2, 41–44. https://doi.org/10.15407/sem2018.02.05
- Перепльотчиков Є.Ф., Василів Х.Б., Вінар В.А. и др. (2018) Підвищення зносотривкості низьклегованої конструкційної сталі плазмово-порошковим наплавленням сплавами на основі заліза, хрому і нікелю. Фізико-хімічна механіка матеріалів, т. 54.- № 3. – с. 81-89.
- Рябцев И.А., Переплетчиков Е.Ф., Бартенев И.А. и др. (2018) Влияние амплитуды и частоты колебаний плазмотрона на химическую и структурную неоднородность металла, наплавленного плазменно-порошковым методом. Автомат. сварка. № 5. – с. 3-8.
- Рябцев И.А., Кныш В.В., Бабинец А.А. и др. (2019) Методики и образцы для сравнительных исследований сопротивления усталости деталей с многослойной наплавкой. Автомат. сварка № 2. – с. 36-41.
- Кусков Ю. М., Жданов В. А., Рябцев І. О. и др. (2019) Шляхи підвищення корозійної тривкості наплавленого під шаром флюсу покриву з високохромистого порошкового дроту. Фізико-хімічна механіка матеріалів. № 5. – С. 90-95.
- Рябцев І. О., Книш В.В., Бабінець А.А. и др. (2020) Втомна довговічність зразків після зносостійкого виготівного та ремонтного наплавлення. Автоматичне зварювання. – № 9. – С. 28-35.